3 ways to optimize warehouse picking routes
A picking route in the warehouse refers to the specific path or sequence that warehouse workers follow to collect items from different locations within the facility to fulfill customer orders efficiently. It involves determining the most optimal route through the warehouse to minimize travel time and maximize productivity. There are ways to optimize your picking routes to ensure efficiency and on-time delivery to your customers.
There are various methods to optimize picking routes in a warehouse, whether through automated processes using a digital WMS or manual strategies. Zone picking helps alleviate congestion in high-traffic areas, while batch picking enables pickers to handle multiple orders simultaneously. Additionally, advanced WMS solutions like Bitlog WMS can automatically calculate the most efficient route based on inventory availability and other key factors.
Ultimately, the quicker and more accurate your order picking process, the more satisfied your customers will be.
Zone Picking
Zone Picking in a warehouse refers to the method of dividing the warehouse into different zones and assigning specific areas to individual pickers. This strategy allows for parallel picking activities, where multiple orders can be picked simultaneously in different zones. By implementing Zone Picking, warehouses can reduce travel time and minimize congestion in high-traffic areas.
In a Zone Picking system, each picker is assigned a specific zone or area of the warehouse to focus on. This specialization allows pickers to become experts in their designated zone, leading to faster and more accurate order fulfillment. Additionally, Zone Picking promotes a more organized and systematic approach to picking, as pickers are responsible for maintaining the inventory within their assigned zone.
By implementing Zone Picking, warehouses can optimize routes, streamline operations, and enhance overall efficiency, especially for high-volume orders or large inventories, leading to successful order fulfillment.
Batch Picking [Trolley or Bins]
Batch picking is a fantastic method that has been proven to optimize the order fulfillment process in warehouses and distribution centers. By grouping items together based on their location in the warehouse and the orders they belong to, workers can pick multiple orders at once using a scanner connected to the application-based WMS.
Not only does batch picking optimize warehouse operations, but it also directly affects customer satisfaction and customer loyalty. By allowing workers to handle multiple orders at once, they can reduce travel time and fulfill orders faster. This means that customers receive their orders promptly, resulting in higher satisfaction levels and potential repeat business.
Picking route optimization in Bitlog WMS
Bitlog WMS utilizes advanced algorithms to analyze order data, inventory locations, and warehouse layout to generate optimized picking routes. These routes are designed to minimize travel time and reduce congestion, leading to faster order fulfillment.
Bitlog WMS provides real-time visibility into order status and inventory levels, allowing for dynamic adjustments to picking routes based on changing demand or inventory availability. This ensures that pickers always follow the most efficient routes to fulfill orders accurately and on time.
By leveraging these features and capabilities, Bitlog WMS helps warehouses optimize their picking routes to enhance productivity, reduce labor costs, and improve overall operational efficiency.
Optimize picking route without a WMS
Of course it's possible to optimize picking routes without a Warehouse Management System (WMS). However, the process can be more challenging but still achievable through manual methods and basic planning. Here are some strategies to apply:
-
ABC Analysis: Prioritize items based on their demand frequency, and store high-demand items closer to the packing area to minimize travel time.
-
Layout Optimization: Organize your warehouse layout logically by grouping similar items together.
-
Route Mapping: Plan out picking routes based on the layout of your warehouse and the location of items. Consider factors such as aisle width, shelving height, and congestion points to design efficient routes.
-
Standard Operating Procedures (SOPs): Develop clear SOPs for picking operations, including guidelines for route planning, order prioritization, and picking techniques. Train warehouse staff to follow these procedures consistently.
-
Performance Monitoring: Regularly monitor picking performance metrics, such as order fulfillment time and picking accuracy, to identify inefficiencies and areas for improvement. Adjust picking routes and procedures accordingly.
While these manual methods can help optimize picking routes to some extent, please note that this requires internal resources for the project to be completed successfully. Most likely more resources than you might expect. However, when in place it helps boost efficiency greatly.
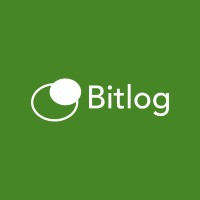
Story by
The Bitlog Team