The five levels of warehouse maturity
A good way to assess the maturity of your warehouse processes and setup is to use a five-stage scale. When we meet with companies that are ready for the next step, they are typically somewhere along this maturity scale.
However, in order to gain efficiency and expand and evolve your operations, your company will most likely need to advance in maturity. When purchasing a WMS, you should consider your warehouse system’s maturity level as well as your business’s needs (now and long-term) and resources.
The five levels of warehouse maturity
While it's crucial to progress your warehouse operations for optimal growth, it's important to note that starting at the initial level isn't necessarily a negative; in fact, it may be the best solution for a smaller warehouse with limited resources. Let's explore the five levels of warehouse maturity below.
In this blog post: |
1. ERP with printed picking lists
At this initial stage of warehouse maturity, the use of an ERP system with printed picking lists is the basic level of system support for warehouse operations. Manual processes are prevalent for stocktaking and receiving goods from suppliers.
While this may be suitable for smaller warehouses with limited resources, it signifies a need for improvement in order to enhance efficiency and productivity. Transitioning from manual processes to more advanced warehouse management systems can streamline operations and pave the way for growth and evolution in the warehouse environment.
Read more and watch the video about Care of Carl's transitioning from paper lists to a WMS >
2. ERP system together with a mobile solution
In this stage, the mobile system is typically linked directly to or integrated with your ERP platform. This integration allows for smoother communication between the systems, providing a more streamlined process for warehouse operations. While you may find yourself limited to the functionalities offered by your ERP system and the ERP WMS module, this setup still offers a cost-effective solution for smaller warehouses with lower volumes.
Although the efficiency improvement may not be significant at this stage, the initial investment required is relatively low, making it a practical choice for businesses with limited resources. However, it's essential to note that as your operations expand, this setup may hinder your potential for growth.
Make long-term estimations and consider the possibility of needing to upgrade or replace your system to accommodate the increased demands of a larger warehouse environment.
3. A WMS solution
A warehouse management system (WMS) can significantly elevate your warehouse operations by seamlessly integrating with a mobile solution, ultimately boosting efficiency and enabling smooth handling of large volumes of users. With advanced features such as optimized picking routes, multi-order picking capabilities, enhanced traceability, and the ability to track key performance indicators (KPIs), your warehouse processes will be streamlined and optimized for maximum productivity.
When considering your WMS options, it is crucial to view it as a long-term investment rather than a short-term solution. While a mobile solution may offer initial cost savings, investing in a robust WMS ensures scalability and adaptability as your business grows.
❗Be cautious of outdated legacy WMS systems that lack regular updates and are installed on-premise, as they can lead to increased Total Cost of Ownership (TCO) over time. By choosing a modern WMS that aligns with your business needs and goals, you can expect to maintain and utilize the system for many years to come, supporting your warehouse operations effectively in the long run.
4. WMS solution with conveyors and/or voice picking
At this stage of warehouse maturity, integrating a WMS solution with conveyor belts can revolutionize your parcel sorting process and optimize the efficiency of picking bin operations. By implementing voice-picking technology, which allows for hands-free operation during picking tasks, you can further enhance productivity and accuracy in your warehouse operations.
While this integration may require a larger initial investment compared to a standalone WMS system, the benefits in terms of improved efficiency and resource savings are significant. The use of conveyor belts and voice picking not only streamlines the sorting and movement of packed parcels but also minimizes errors and reduces labor costs associated with manual handling.
Investing in these advanced technologies demonstrates a commitment to continuous improvement and innovation in your warehouse processes, positioning your company for future growth and success in the competitive market. By leveraging these cutting-edge solutions, you can stay ahead of the curve and optimize your operations for maximum productivity and customer satisfaction.
5. WMS solution for conveyors and picking automation
Integrating a WMS solution with cutting-edge automation technologies like AutoStore or robotic systems at this stage of warehouse maturity can truly revolutionize your warehouse operations. By implementing goods-to-man features that minimize walking distances and maximize picker efficiency, you are taking a significant step towards enhancing productivity within your warehouse. This advanced integration may require a substantial initial investment, but the potential benefits in terms of operational efficiency and cost savings are truly remarkable.
With these innovative technologies in place, your business is not only poised for increased success but also for heightened competitiveness in the market. By embracing automation and advanced picking solutions, you are setting the stage for streamlined operations, improved accuracy, and ultimately, greater customer satisfaction. This strategic investment in cutting-edge technologies will undoubtedly position your company as a leader in the industry, paving the way for future growth and expansion.
Read more and watch the video about Nordic Nest building a warehouse for the future >
FAQ: Warehouse Maturity
Question: Can you provide specific examples or case studies of companies at each stage of warehouse maturity?
Answer: We work closely with companies across the entire spectrum of warehouse maturity levels. Our customers usually falls within stages 3-5 of the scale. Here are some inspiring examples from our customer stories (video + text): Nordic Nest (stage 5), Matsmart (stage 4), and Care of Carl (stage 3).
Question: What are some common challenges that companies face when transitioning between different stages of warehouse maturity?
Answer:
-
Resistance to change from employees accustomed to existing processes.
-
Integration issues when adopting new technology or systems.
-
Resource constraints, such as budget limitations or staffing shortages.
-
Lack of buy-in or support from key stakeholders within the organization.
-
Difficulty in aligning warehouse operations with overall business objectives.
3. Question: Are there any recommended strategies or best practices for companies looking to advance from one stage of maturity to the next?
Answer:
-
Conducting a thorough assessment of current warehouse processes and technology to identify areas for improvement.
-
Developing a clear roadmap or plan for implementation, including timelines, resource allocation, and key performance indicators (KPIs) to measure success.
-
Investing in training and development programs to ensure employees are equipped with the necessary skills and knowledge to adapt to changes.
-
Establishing regular communication channels to keep all stakeholders informed and engaged throughout the transition process.
-
Leveraging the expertise of external consultants or industry experts to provide guidance and support in implementing new initiatives.
Discover how Bitlog WMS can seamlessly integrate with your warehouse operations. Let's talk!
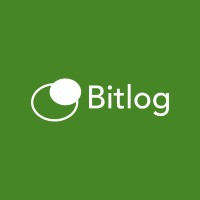
Story by
The Bitlog Team