Apohem: 240% increase in order picking speed in four months
About Apohem
Apohem is an online pharmacy dedicated to making health and skincare accessible to everyone without it being costly or complicated. They are also one of Sweden's fastest growing e-commerce businesses.
With prescription management and over 16,000 items in stock, inventory management is a key focus for Apohem, with reliability being a top priority. Upon moving to their own warehouse located in Årsta, just outside Stockholm's city center, the need for a Warehouse Management System (WMS) arose, leading Apohem to choose Bitlog.
Since Apohem decided to bring their warehouse management in-house from their previous 3PL provider, demand has skyrocketed. With Bitlog WMS, they have implemented a warehouse system tailored to their operations that has exceeded everyone's expectations.
At present, plans are in motion to relocate their warehouse operations to a new site. With 25,000 square meters of warehouse space in Kallhäll, north of Stockholm, this move represents Apohem's next venture, offering significant potential for further business expansion.
"[Before Bitlog] we encountered operational challenges with reliability and scaling up in volume."Anette Mühlbach, Head of Logistics & Purchasing, Apohem |
Installation
LocationKallhäll (Stockholm), Sweden |
In this videoAnette Mühlbach Therese Mella |
Challenge
Before partnering with Bitlog, Apohem had to juggle multiple workflows, with prescription handling managed internally by licensed pharmacy technicians, and all other inventory management outsourced to a third-party logistics provider (3PL). This setup made it challenging to consolidate orders as they were picked using different WMS systems and in different parts of the warehouse.
At times, they found it difficult to be efficient when needing to scale up inventory management as demand rapidly increased. There was also an underlying concern for operational reliability since Apohem prides itself on fast deliveries, especially for prescription medications. The system must never be down.
"One of the issues we encountered was operational reliability and scaling up in volume," shared Anette Mühlbach, Logistics & Purchasing Manager at Apohem.
For Apohem, it became crucial to find a partner that could work with real-time order data, provide clear and robust APIs, and provide excellent performance, reliability, and scalability. They needed a partner to collaborate with on developing products that solve their challenges.
Apohem visited a customer warehouse before choosing Bitlog WMS"We had the opportunity to test Bitlog WMS firsthand during a reference visit. We gained hands-on experience by delivering goods and picking and packing with the tools we use in our work today."Anette Mühlbach, Head of Logistics & Purchasing, Apohem |
Solution
When Apohem began their search for WMS providers, they quickly compiled a shortlist of vendors to engage in further discussions. Many providers were disqualified early on as they were deemed unable to support Apohem's rapid growth. One of the key factors that led to Bitlog being chosen was the reference visit they had the opportunity to conduct at one of our customer's warehouse.
"We had the opportunity to test Bitlog WMS firsthand during a reference visit. We gained hands-on experience by delivering goods and picking and packing with the tools we use in our work today," shared Anette.
She continued to explain that it quickly became evident that Bitlog was a competent WMS system that is fast and easy to get started with.
"As a pharmacy, we need traceability in all our transactions," said Therese Mella, Head of Supply Chain Development at Apohem, adding, "and it also needs to be quick to get started with picking orders."
Another crucial factor on Apohem's requirements list was that the new WMS system had to be reliable.
"We operate two shifts during the week, as well as shifts on weekends. We have production running all the time," explained Therese.
"When we started working with Bitlog WMS, we set a goal of 100 order lines picked per hour within a year. We achieved that in four months."Anette Mühlbach, Head of Logistics & Purchasing, Apohem |
Strong collaboration for continued development
It was crucial for Apohem to find a partner who listens to their customers and incorporates feedback into product planning. Apohem sought a partner they could collaborate with to develop a user-friendly solution.
"We chose Bitlog over other competitors because we needed a partner to work with us to develop new solutions and continuously improve the WMS," shared Anette.
At Bitlog, collaboration with our users is something we take immense pride in. More than 50% of all new product development happens in consultation with our customers or based on customer requests.
Proposal Planner (Bitlog WMS module)
The Proposal Planner is a feature developed collaboratively by Bitlog and Apohem. This tool supports high-growth businesses by helping to manage and prioritize picking queues based on various criteria such as order cut-off time, order placement time, carrier, or even down to a detailed level.
This functionality empowers you to create the most efficient picking queues for your warehouse.
"The right order at the right time," says Therese.
Image: Apohem's iconic blue boxes ready to be shipped to customers.
Results
Since the implementation of Bitlog WMS at Apohem, along with the relocation to a new, spacious warehouse in Årsta just outside Stockholm's city center, they have found it easier to prioritize and plan their warehouse operations.
"Bitlog understands our business, and we always develop things together," Therese comments on the collaboration.
When the planning of the WMS investment began, there was a hope to achieve 60 order lines picked per hour. This number was quickly adjusted to 100 in preparation for the partnership with Bitlog:
"When we started working with Bitlog WMS, we set a goal of 100 order lines picked per hour within a year. We achieved that in four months. Currently, we are at around 140-145 order lines picked per hour, with some employees reaching over 240 order lines per hour, showcasing incredible efficiency in picking."
The outcome of implementing Bitlog WMS and utilizing the application in operation has resulted in a 240% increase in the number of order lines picked than initially estimated. Some employees have even seen close to a 400% increase, a remarkable achievement that validates Bitlog WMS as the right choice for Apohem's warehouse.
Together, we have a clear roadmap of functionality and enhancements that can shave off seconds from all aspects of Apohem's warehouse processes to further boost efficiency. Only time will reveal how much Apohem can streamline its warehouse, and we are extremely proud and delighted to be part of their meteoric journey.
You might also like:
-
Care of Carl >
-
Nordic Nest >
-
Hutalfors Group >
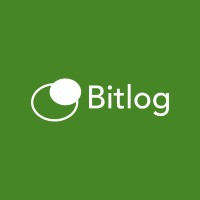
Story by
The Bitlog Team